Today’s food and beverage production demands a digital filling line solution that can deliver a highly accurate monitoring system for information management that may be remote but is always using real time data in order to optimise operations and improve productivity. SIG's answer to this is combiLink – a single and flexible information management solution for filling line operation.
Food and beverage production is becoming more challenging, with filling plants facing higher demands, greater competition and ever shorter production cycles. All too often, manufacturers are faced with multiple reporting systems, outdated data, manual data collection and a lack of filling line insights.
By connecting every machine in a filling line, SIG’s combiLink collects unlimited data and shows it in preconfigured or personally designed reports. Customers can view charts showing operational and technical efficiency and view downtime incidents from their desktops, tablets or smartphones. Smart notifications can alert the team to incidents so avoiding bottlenecks and costly downtime.
“56% of companies intend to increase efficiency by more than 20% over the next 5 years,” said Ayed Katrangi, Senior Product Manager Automation and Digitalization at SIG. “combiLink can make a decisive contribution to this. It is a smart factory solution that offers a completely new way of monitoring and analysing the efficiency and productivity of a filling line, enabling customers to take on-time decisions fast and to automate operations to meet the needs of Industry 4.0, improve filling line OEE and optimise TCO, based on ISO 2240 standards.”
With the same connectivity used in IoT applications, combiLink seamlessly connects every machine in a filling line. This means producers get a single end-to-end window to view current and historical levels of efficiency and performance, while also seeing where improvements can be made in the future. combiLink’s connectivity is based on the latest industrial communication standard OMAC, enabling it to collect unlimited data over OPC UA technology from every machine and store it securely.
combiLink can also send out data to MES, ERP and other business intelligence systems. Its open architecture and standards-based interface connect easily to third party applications such as cloud based systems and predictive analysis tools. This two way communication enables unlimited operation applications with the option of customer plug-ins.
Turning the challenges of high speed production into reality, SIG’s smart factory solutions underline its commitment to constant system innovation always bearing the latest customer needs in mind.
combiLink is just one example of how SIG can design and engineer the most advanced and intelligent end to end plants using IoT-enabled systems, data and automation, ensuring that customers can monitor and optimise operations, with rapid intervention for best results.
About SIG
SIG is a leading systems and solutions provider for aseptic packaging. We work in partnership with our customers to bring food products to consumers around the world in a safe, sustainable and affordable way. Our unique technology and outstanding innovation capacity enable us to provide our customers with end-to-end solutions for differentiated products, smarter factories and connected packs, all to address the ever-changing needs of consumers.
Founded in 1853, SIG is headquartered in Neuhausen, Switzerland. The skills and experience of our 5,000-plus employees worldwide enable us to respond quickly and effectively to the needs of our customers in more than 60 countries. In 2017, SIG produced 33.6 billion carton packs and generated €1.66 billion in revenue. For more information, visit www.sig.biz.
COMBILINK VIDEO:
https://www.youtube.com/watch?v=iQqP2yP4DOQ
MORE ABOUT COMBILINK ON OUR BLOG:
https://www.sig.biz/signals/en/articles/unlocking-filling-line-potential
SIG’s combiLink is a smart factory solution that offers a completely new way of monitoring and analysing the efficiency and productivity of a filling line, enabling food and beverage producers to take rapid decisions and optimise operations whenever necessary.
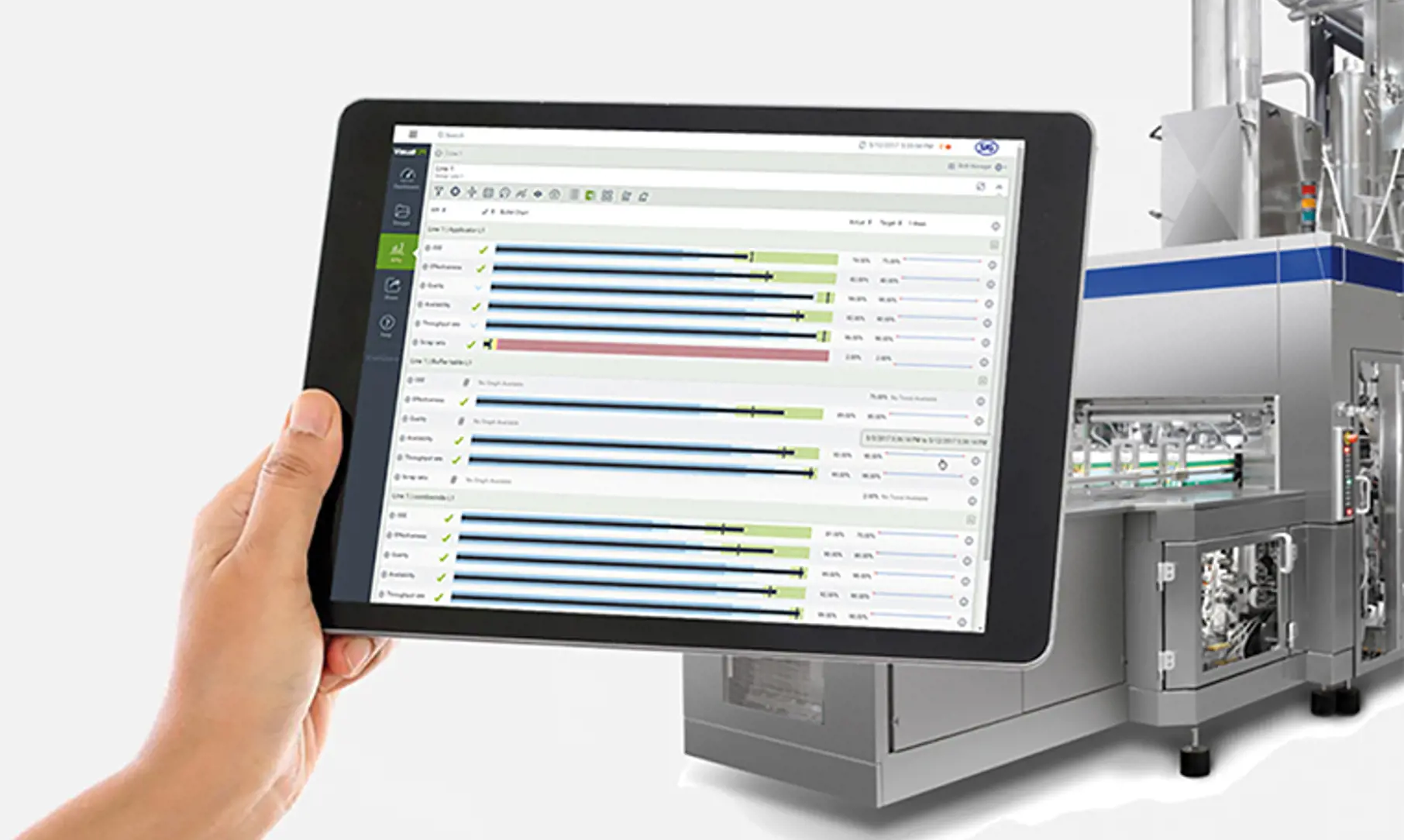