Our goal at SIG is to provide a total packaging solution perfectly tailored to our customers’ needs. For decades, we’ve been on the cutting-edge of films, fitments, and equipment and have helped hundreds of companies design flexible packaging that is sustainable and cost effective.
Our equipment lineup—which includes a variety of machines outfitted with a range of different filling technologies—allows us to design a total packaging solution focused on responsible manufacturing. The solutions we engineer give our customers measurable cost savings while emphasizing waste reduction by bringing production in-house.
A filler for every need
No matter where you are on your packaging journey, we have a filler that’s perfect for you. Our equipment is designed to meet you where you’re at, and can be adapted to reflect the unique needs of your business.
HFFS: a leader in efficiency
Our horizontal form-fill-seal machines (HFFS) make and fill packages all on one machine. Starting from pre-printed film rolls, HFFS machines form, fill, and seal pouches efficiently and at a consistent packaging rate. HFFS machines are easy to clean and provide a quicker production rate compared to machines that utilize pre-made packaging.
We offer a wide range of HFFS machines adaptable to your company’s needs. We offer machines that can produce sachets and pouches, both with and without fitments.
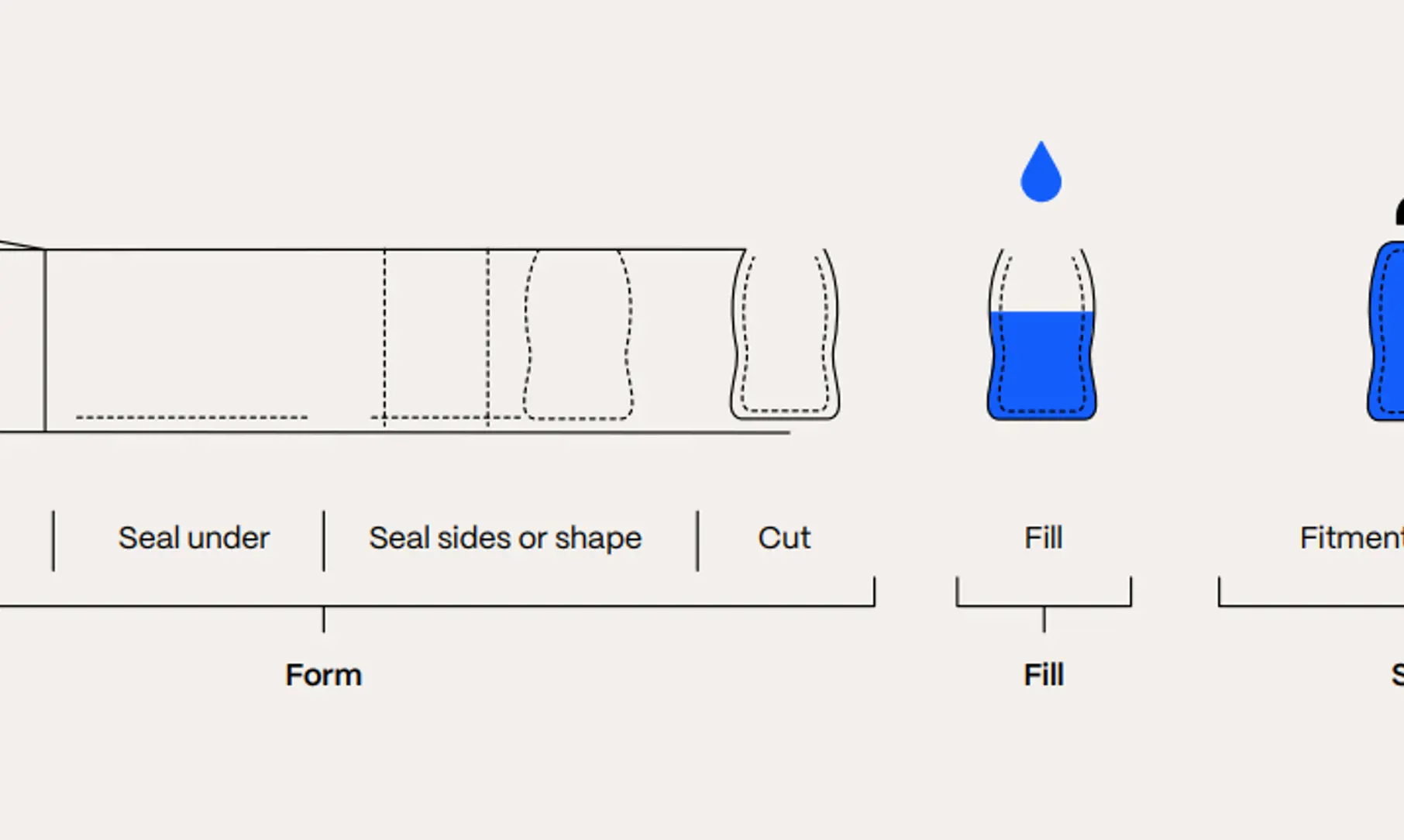
Hybrid: the flexibility to do more
Hybrid machines separate the production process into two steps: forming and sealing on one machine with filling on another.
You can maximize the benefit of having both an on-site packaging production machine along with the accuracy of a filling machine working with your pre-made packages—both lines work independently to increase productivity. These machines are great if you have multiple shapes and sizes of products to fill on the same line.
Hybrid machines fill through the spout, meaning that the pouch is filled right to the top, reducing headspace in the product.
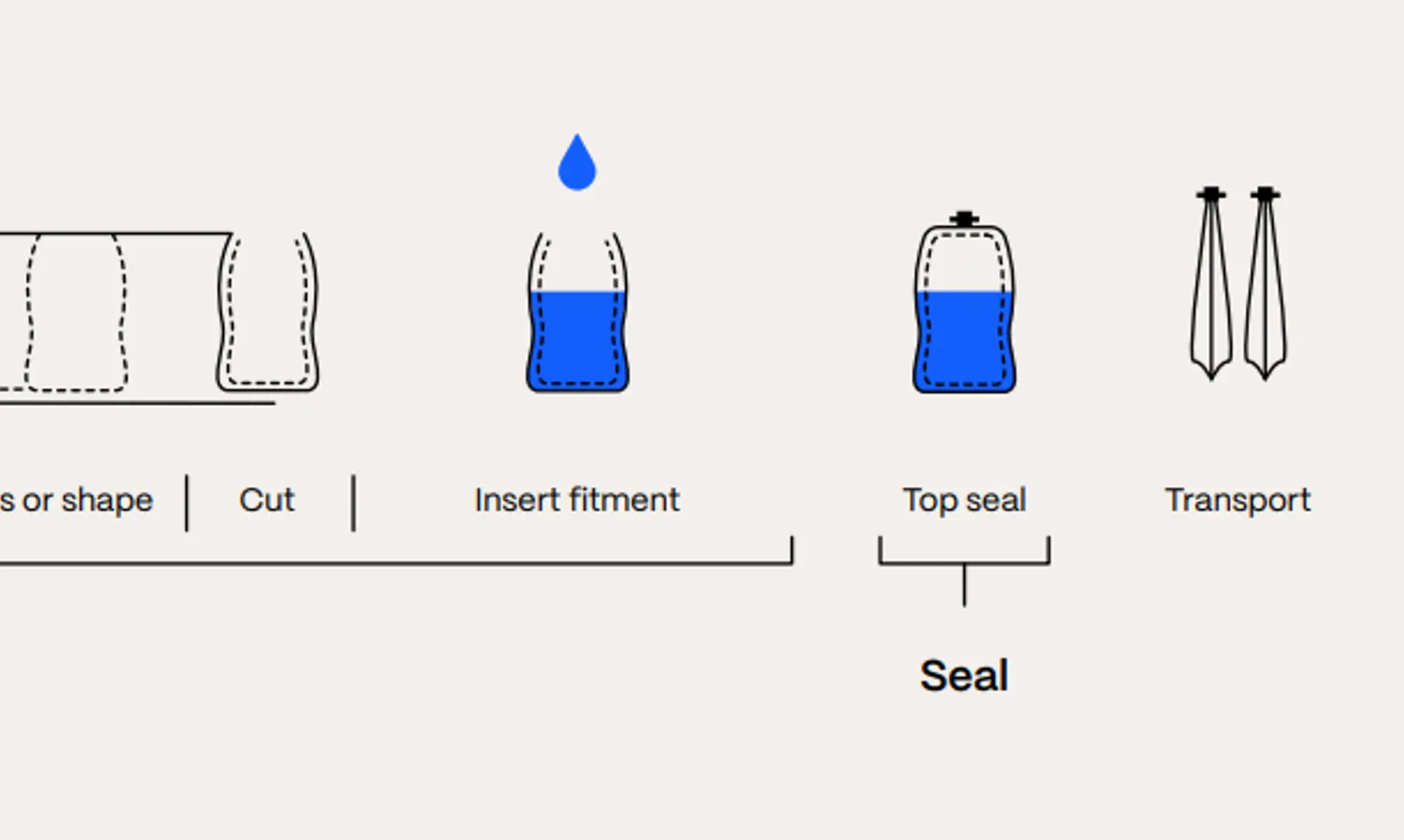
Key advantages
- Flexible: because the forming and filling happen independently, companies have the flexibility to operate machinery based on their needs—ideal for companies that have multiple products in their catalog
- Precise: the filling end of a hybrid machine is a continuous motion filler, meaning there’s more time spent in filling, providing a higher level of accuracy
- Reduced waste: hybrid machines create less headspace, meaning packages are filled to their capacity
- Consistent: packages are consistently made and filled from one pouch or bag-in-box to the next
- Applicable for bag-in-box: can be used for a variety of formats, including bag-in-box
Pre-made: simplifying your production line
We offer a line of filling machines designed for pre-made pouch and bag-in-box packaging. Our pouch fillers use a rail system, giving brands eager to enter the spouted pouch market an easy access point without an initial costly investment.
We provide pouches on rails for you and the machines operate on a continuous filling motion, allowing for longer fill times while translates to more accuracy and less product splash. For bag-in-box, we ship customers webbed bags that are easy to load and make for quick and simplified filling.
Our SureFill and TrueFill fillers are designed specifically for bag-in-box and pouches, which allows them to be highly accurate and consistent.
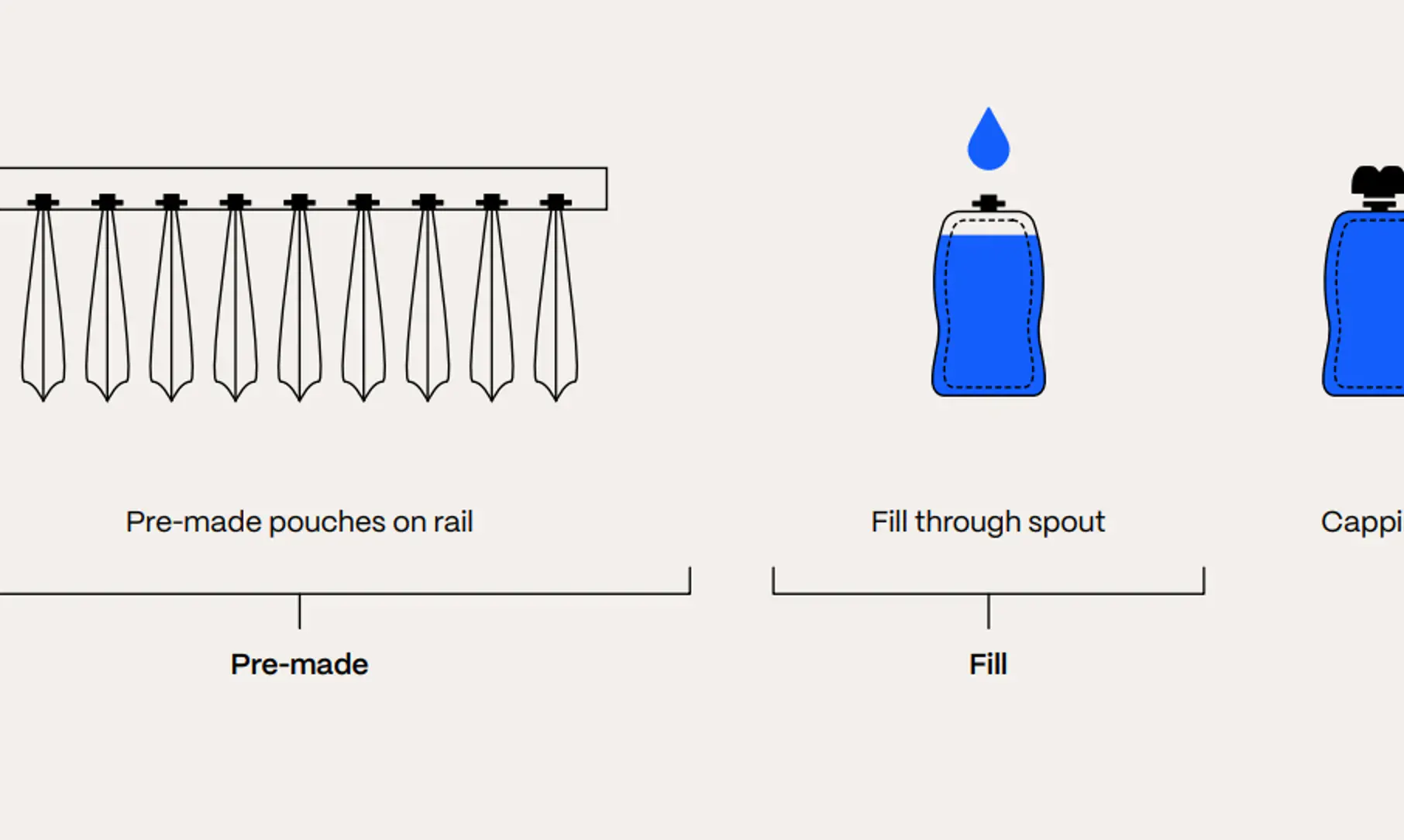
Key Advantages
- Maximized expertise: SIG is known for market-leading pouch and bag-in-box technology, so companies can rely on packaging that comes ready to use
- Simply flexible: for people looking to enter the pouch market or other emerging markets, a pre-made filler breaks down the barrier to entry
- Safe: pouches and fitments are made in clean environments
- Proven effective: we use the same automated equipment we sell to consumers because we know it makes packaging formats that are intact and ready to use
At the forefront of filling technology
Our filling machines boast a variety of options and technologies that can adapt to your current or future needs. We invest in research to develop sealing and filling innovations that are sustainable without compromising on quality. All sealing and filling options are available for any of our filling machines.
Sealing options
- Heat seal—a classic sealing option, this works by utilizing electric resistance and is reliable and cost-effective. There is a cooling step needed when using this option, increasing your environmental footprint.
- Ultrasonic seal—also known as cold sealing, this works by using high-frequency vibrations to seal the packing due to molecular vibration. Ultrasonic seals are done hermetically, seal quickly, and use less packaging material since the sealing area is significantly decreased
- Induction seal—this is a revolutionary sealing technology that generates heat with an electro-magnetic field. It cuts sealing time by one-third compared to heat sealing and can be used on any film structure, making this the most effective and sustainable sealing option.
Filling options
- Hot-Fill—This is for high-acid products: the product is heated for a predetermined amount of time to sterilize and the package can then be held without refrigeration.
- Fresh—Popular for products with dairy, this system uses cold to kill bacteria and doesn’t required added preservatives to keep food safe
- Ultra-Clean (ESL)—Intended for items in cold chain with a short shelf life, ultra-clean filling uses laminar flow, UV lamps, and/or hydrogen to sterilize.
- Aseptic—Aseptic packaging pairs commercially-sterile products with pre-sterilized packaging. The package is hermetically sealed and is shelf stable.
Decades of equipment technology and innovation
To produce fully integrated filling systems, the equipment is just one piece of the puzzle. Our machines represent years of research, a dedicated team of technicians and customer service staff, and a continued drive to always improve on our ideas.
Every decision we make comes back to sustainability: we design machines built to last because we don’t want to see them traded in a few years down the line. We make films and fitments that cut down on raw materials so each part of your flexible package has been thoroughly considered and improved upon.
We’ve worked in partnership with Purdue University to invest in the next generation of filling technology, and have a Materials Science Lab on-site that rigorously tests new materials and adheres to strict protocols for assessing the safety, usability, and durability of every product we make.
Our filling machines have the power to significantly reduce your environmental footprint, while offering a staggeringly quick return on investment. Get in touch with us today about filling machine options for your company.
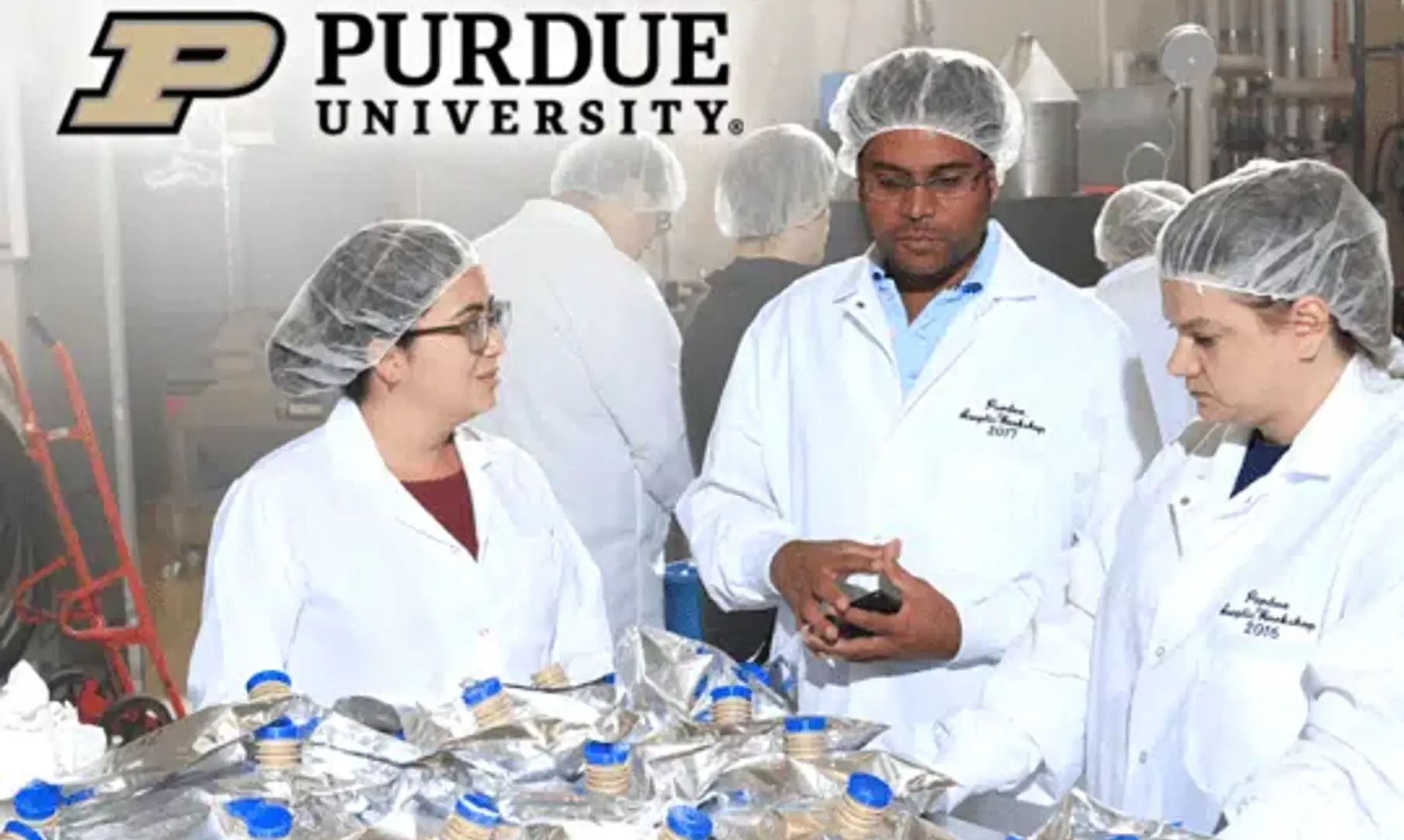
- luglio 01, 2022
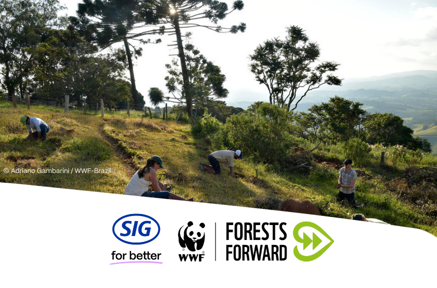
How WWF and SIG, together with 25 other leading companies, are working to help forests thrive
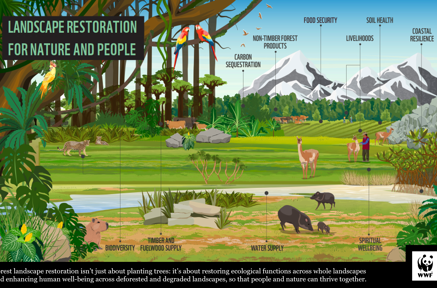
Beyond tree planting
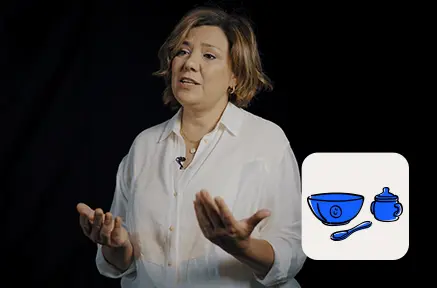